What Is Lean Manufacturing? Meaning, Benefits & How to Reduce Waste
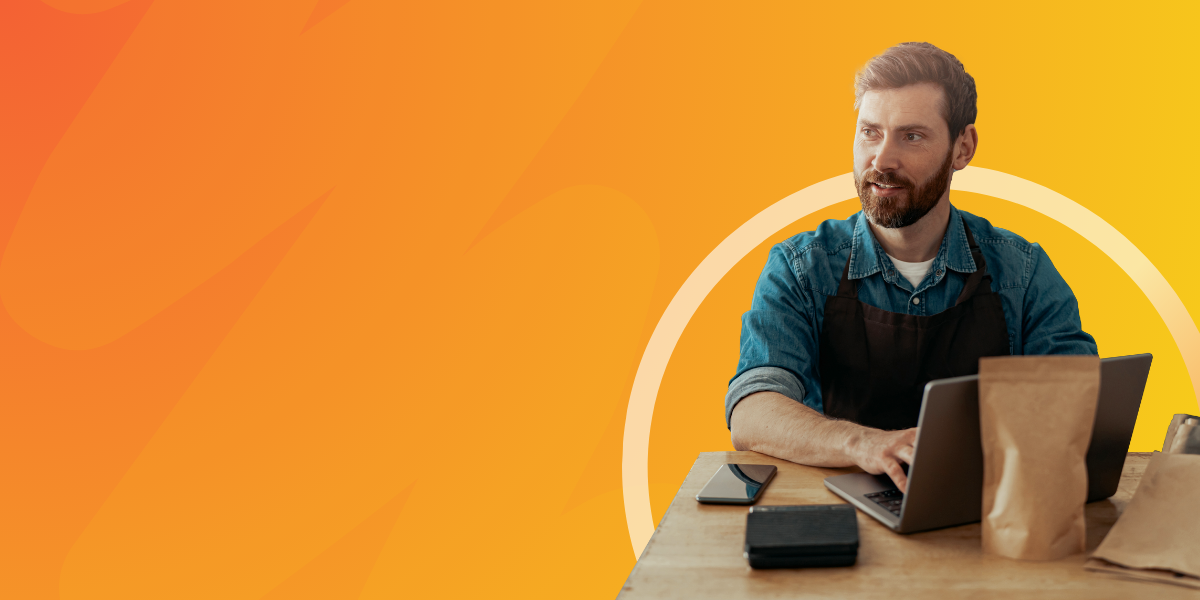
Waste is a problem—especially in the manufacturing industry.
According to the EPA, manufacturers produce 1,800 pounds of waste per employee. That’s a lot of defective products, cardboard boxes, and plastic packaging that ends up in landfills.
Of course, physical waste isn’t the only kind of waste out there. Unfortunately, manufacturers also waste time and energy on a regular basis. Lean manufacturing processes are the answer.
In this guide, we’ll explain what lean manufacturing is, lean production principles you need to know, the types of waste found in most manufacturing plants, and how to eliminate both physical waste and non-value activities from your production process. Let’s get started!
Definition of Lean Manufacturing
First things first, what is lean manufacturing?
Lean manufacturing is a management philosophy that aims to eliminate waste throughout the production process. It does this by focusing on continuous improvements.
In other words, lean manufacturing operations remove everything that does not add value. This often leads to greater productivity levels, lower costs, and better products.
History of Lean Manufacturing
Lean manufacturing concepts have been around for centuries. But Shigeo Shingo and Taiichi Ohno first formalized the process when they worked for the Japanese company, Toyota.
Authors James Womack, Dan Jones, and Daniel Roos then wrote about the “Toyota production system” in, The Machine That Changed the World, and popularized lean manufacturing.
Since that time, countless companies have worked to achieve continuous improvement, eliminate waste, and build lean manufacturing plants that produce better margins.
Importance of Lean Manufacturing in Today’s Industry
As described above, lean manufacturing concepts will help your company boost productivity, cut costs, and create better products. Let’s explore these benefits in greater detail:
- Productivity: Lean manufacturing systems aim for the complete elimination of waste. Inefficient activities that destroy worker productivity levels fall into this category. Want to get more done in less time? Commit to a lean production system.
- Cost Efficiency: Lean production has financial benefits, too. Once your manufacturing plant adopts these principles, you’ll boost productivity levels (see above) and minimize overproduction issues. Both of these things will help your plant reduce costs.
- Better Products: Finally, lean manufacturing techniques lead to better products. This makes sense. When you focus on continuous improvement throughout the production process, the end product should be more desirable to target customers.
The Lean Six Sigma Concept
We’d be remiss if we didn’t talk about Lean Six Sigma…
In 1986, American telecommunications company, Motorola, created the Six Sigma strategy. The objective was to reduce process defects and streamline the variability of production procedures.
Here’s the cool part: lean manufacturing and Six Sigma concepts can be combined to create Lean Six Sigma. In theory, this methodology helps companies reduce waste and process defects, which will enable them to achieve peak operational excellence.
Lean Six Sigma methodology can be segmented into five distinct phases:
Define: Decide which process you want to improve and its current problems
Measure: Study how the process performs and the current magnitude of problems
Analyze: Identify the root cause of the problem caused by the existing process
Improve: Determine ways to solve the root cause of the problem and fix the process
Control: Work to maintain the solutions you’ve implemented into your process
By going through these five phases, you’ll be able to eliminate waste and defects from your manufacturing process. This will lead to greater productivity and fewer costs.
Key Lean Manufacturing Principles to Know
The famed Toyota production system that inspired the lean manufacturing revolution is built on five pillars. These pillars, referred to in this article as lean manufacturing principles, are:
Identify Value
Manufacturers create value, but consumers define it.
So ask yourself, “What value do our customers place on our products?” Just as important, “How much are potential customers willing to pay to acquire the value we provide?”
Lean principles encourage manufacturers to accommodate customer requests and achieve customer satisfaction. This can be done by eliminating waste so that the right products can be created in cost-effective ways. When this happens, lean management is considered a success.
Map the Value Stream
The term “value stream” refers to the steps your manufacturing plant takes to produce products. Said steps should include everything from “obtain raw materials” to “deliver final product”.
Lean processes help manufacturers analyze their value streams. The goal? To identify and eliminate waste throughout the entire production cycle.
(Note: modern manufacturing value streams are often complex. You’ll likely need input from the entire supply chain—including engineers, designers, etc.—to adhere to lean principles.)
Create Flow
What stands between your manufacturing plant and a finished product?
Lean manufacturing principles help users remove these barriers and create a continuous flow. That way products are created in less time and with less hassle than before.
A well-designed product flow will enable your company to eliminate wasted time and money. As such, it’s a critical component of the lean manufacturing process.
Establish a Pull System
Let’s talk about the difference between a push and pull system.
Push systems are used by manufacturing resource planning (MRP) tools to determine inventory levels. Products are then manufactured to meet these forecasted amounts.
Pull systems, on the other hand, wait until there is demand to manufacture products. While this may lengthen response times, it helps eliminate waste, which is crucial to lean production.
Lean thinking dictates you establish a pull system for your company. This is fairly easy to do with the right lean manufacturing tools—even simple ones such as kanban cards.
Pursue Continuous Improvement
Last but not least, find opportunities for improvement.
Lean manufacturing requires manufacturers to strive for better. Ask yourself questions like, “Are we doing the best we can?” And “Where should we focus our improvement efforts?”
Lean management is a continual process because reducing waste isn’t a one-time job. You’ll need to test different ideas and techniques to find the optimal manufacturing process.
Types of Waste in Manufacturing Processes
We’ve talked a lot about waste and why your manufacturing plant should eliminate it. But we haven’t talked about specific kinds of waste to look out for. Let’s do that now:
Defects
Poorly made products are probably the most obvious type of waste in the manufacturing industry. A lean manufacturing process will improve quality control and help you limit items made with the wrong materials, broken pieces, incorrect wiring, and similar scenarios.
Lean production will also help your team avoid shipping products that don’t include proper documentation, as these items are often sent back for refunds.
Waiting Time
True to its name, waiting time waste happens when people or machinery have to wait to complete the next step in a manufacturing process. This category includes:
- People waiting for machines
- Parts waiting to be assembled
- Products waiting to be shipped
- Idle equipment waiting to be used
Lean manufacturing strategies will help speed up production times so that workers aren’t waiting for the equipment they need to do their jobs. It will also help workers reach peak productivity so that parts never wait to be assembled, products never wait to be shipped, etc.
Transportation
Unnecessary transportation can lead to waste as well.
When it comes to lean manufacturing, transportation waste refers to the movement of people, products, or tools that could have been avoided with better planning.
Does your manufacturing process have extra steps? Do workers have to walk back and forth inside your factory to complete a finished product? Do you have multiple storage facilities?
These are all examples of transportation waste because they cost your company time and money. They can also lead to employee injuries, which are not only expensive, but can damage your company’s reputation in the marketplace. A bad rep is rarely a good thing.
Inventory
Inventory might not seem like a waste. After all, you need inventory to meet demand, drive revenue, and satisfy customers, right? You can’t do that if you don’t have products to ship…
Inventory that flies off the shelf is a good thing. Inventory that sits in your warehouse is considered waste because it costs money to produce and store, but doesn’t generate a return.
Inventory waste is often caused by inaccurate sales forecasting, an unreliable supply chain, bulk ordering (even when discount pricing is accounted for,) and the overproduction of parts and/or complete products. Fortunately, the lean production process can help minimize inventory waste.
Inventory waste problems can also be solved with sales forecasting tools which are included in many CPQ solutions. B2B ecommerce strategies can help too, as spare parts can be sold to consumers around the world, instead of collecting dust in your warehouse.
That’s not to say that lean manufacturing is unnecessary. Rather, lean manufacturing principles can be implemented alongside the right software platforms to eliminate inventory issues.
Motion
Motion kills time and wears down equipment. As such, it’s a type of waste that you’ll try to eliminate once you adopt a lean philosophy. Motion waste often looks like:
- Machines completing extra steps
- Employees over-reaching for parts
- Products being moved multiple times
Motion waste and transportation waste are similar. Think of it like this: motion waste refers to unnecessary small-scale movements, while transportation waste refers to unnecessary large-scale movements. Both should be eliminated for truly lean production to emerge.
5 Ways to Eliminate Waste and Non-Value Add Activities
Ready to adopt lean manufacturing principles and build your own Toyota production system? The five best practices below will have you eliminating waste in no time!
1. Set SMART Goals
Lean manufacturing can help your workers become more productive, your company save money, and your customers enjoy better products that encourage loyalty.
But these things will only happen if you take a systematic approach when implementing lean practices. So, before you do anything else, choose SMART goals to achieve.
SMART is an acronym that stands for:
- Specific: Know what you want to accomplish
- Measurable: Choose KPIs to track progress
- Achievable: Select a goal you can complete
- Relevant: Tie your goal to company objectives
- Time-Bound: Set a deadline to reach your goal
For example, “Our manufacturing plant will reduce waste by 25% in the next three months.”
Once you have SMART goals in place, you and your team will know exactly what to work towards. You’ll also be able to track progress and properly assess your production process.
2. Audit Your Entire Supply Chain
Now that you know what your waste management goals are, audit your supply chain. The objective? To find and eliminate all forms of waste via lean thinking principles.
For instance, your workers might walk long distances to retrieve items. Or mismanage their time and leave machines idle. Or produce more products than they need to.
Now, you can conduct this kind of audit yourself. But you might want to hire an external firm to do it for you, as this will reduce your team’s workload and help you obtain a green certification.
3. Prioritize Inventory Management
Does your company have excess stock? Do your factory workers produce more products than your sales team can sell? These problems can be solved with inventory management.
Bulk pricing seems like a great idea—until you have to warehouse hundreds of parts that you won’t be able to use for a long time. Since warehouse space costs money, this is a form of waste that should be minimized. Commit to lean manufacturing and only order what you need.
Also, analyze your production flow. Why do your workers produce more products than required? Do they need better training or is there a flaw in your system? Find the problem and fix it.
4. Create a Preventive Maintenance Schedule
Broken equipment is a disaster for manufacturing plants. Not only are these machines expensive to fix, but they can also lead to delays in the lean manufacturing process.
Fortunately, preventive maintenance will help your equipment run for longer.
So, put a preventive maintenance plan in place. That way your equipment is serviced on a regular basis and you avoid major breakdowns. To ensure your manufacturing plant sticks to the maintenance plan, use lean tools to track when machines need to be repaired.
5. Re-evaluate Your Packing Processes
Last but not least, take a serious look at your packing procedures.
Less packaging will reduce costs. It will also make your workers more productive, as they won’t have to stuff so many materials into every box they ship from your warehouse.
You might think about using eco-friendly packaging, too. This will make your manufacturing process more sustainable and reduce waste in the world, not just your plant.
At the end of the day, you need to pack and ship products responsibly. Don’t reduce packaging to the point where products get damaged in transit. Instead, look for simple ways to minimize the materials you use. Then try to make them as green as possible.
Elevate Your Business With a Lean Manufacturing Process
Lean manufacturing processes will improve team-wide productivity levels, while helping your manufacturing company reduce costs and delight customers. Win!
Do what you can to identify waste and eliminate it from your supply chain. You can do this by managing your inventory, committing to preventive maintenance, re-evaluating your packing procedures, and implementing the other tips we shared above. Trust us, it will be worth it.
Looking for additional ways to improve your manufacturing plant? Level up your sales processes with Experlogix. Our platform has all of the tools you need to reduce waste:
- CPQ Software: Create custom rules and access embedded logic features to create more accurate product configurations. Doing so will eliminate waste caused by faulty products, which can lead to $50k in wasted materials and labor costs.
- Document Automation: Digitize your paper-based processes and communicate with clients and customers in more productive ways. With Experlogix, you can easily create proposals, invoices, and other documents and eliminate time-related waste.
- Digital Commerce: Sell products over the internet—directly from your company’s website. Not only will this help you connect with more customers and grow revenue, but it will also give you a viable way to offload spare parts from your warehouses.
Sign up for a free demo of Experlogix today to see if it’s the right tool for your business!